IBG HydroTech GmbH
Mixing plant | Swap body
Mixing plant | Swap body
The IBG Hydro-Tech mixing plant
Description and tasks of the production example (see photos):
The mixing plant stores, tempers and mixes resin and hardener, or component A and B. The components are stored in 4 IBC's. Filling is done either by refueling the contained IBC's or by replacing the empty IBC's with full ones.
The resin can be kept above a temperature determined by the operator with an automatic system. 2 circuit heaters, one for resin and one for hardener, provide uniform temperature. With a movable static mixer, both components can be filled into the pipe liner in a user-friendly way. 2 vacuum pumps with a total of 6 vacuum connections ensure better distribution of the resin.
The calibration roller ensures an exact adjustment of the pipe liner. The filling level of the IBC's is monitored in real time.
The PLC graphic (see photo 3) shows a production example of a graphical user interface. Here, operators can immediately see the positions of the shut-off valves.
The correspondingly set program, e.g. circuit, mixing or filling.
Measured variables are recorded, concentrated and clearly displayed, e.g. temperature, weight or volume, pressure, but also faults or important information and warnings.
The operator gets a clear overall picture of the plant at a quick glance.
Two air-conditioning units are installed in the mixing plant. These are there, on the one hand, to cool the resin a little.
On the other hand, they are also there to make the operator's work as comfortable as possible, even at high or low temperatures.
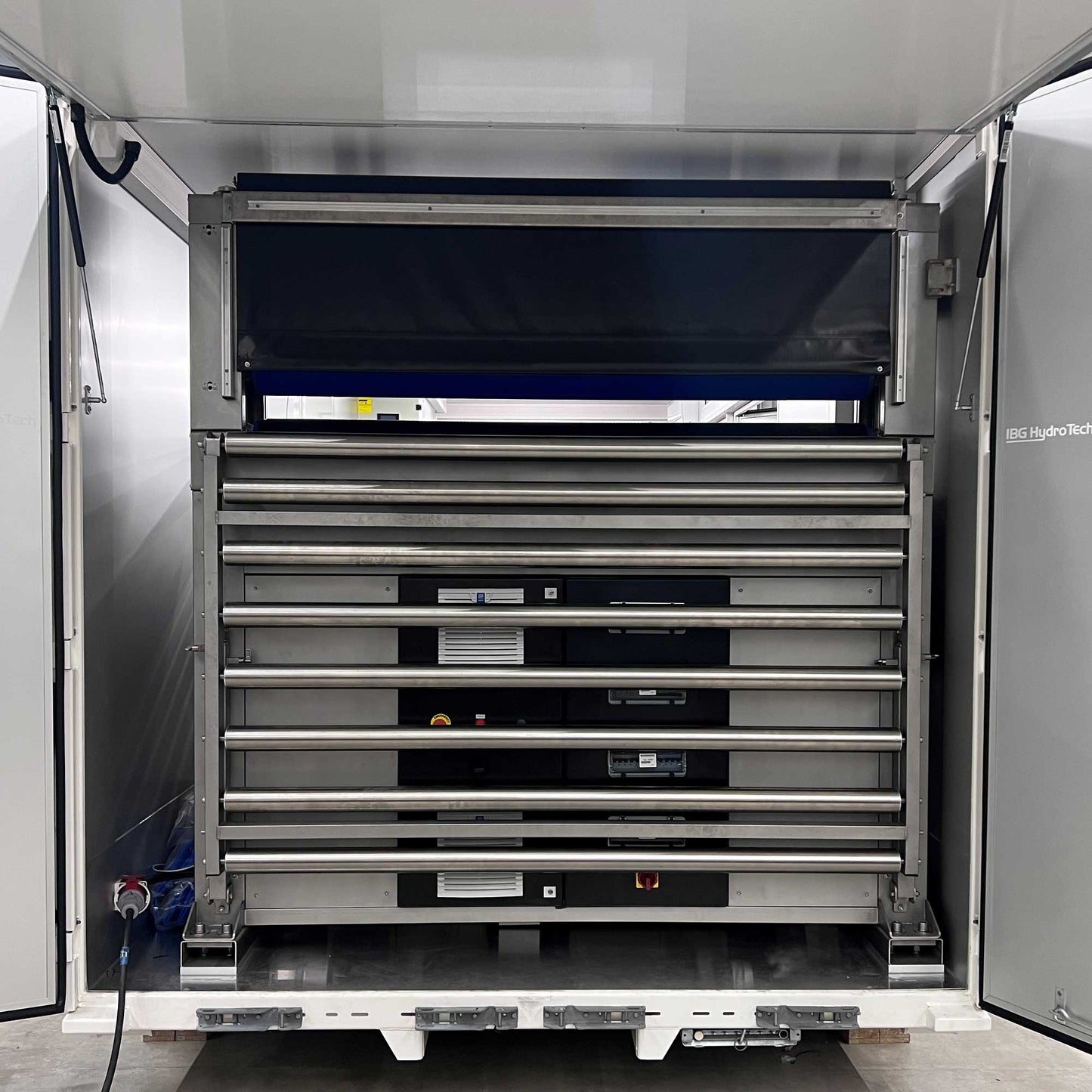
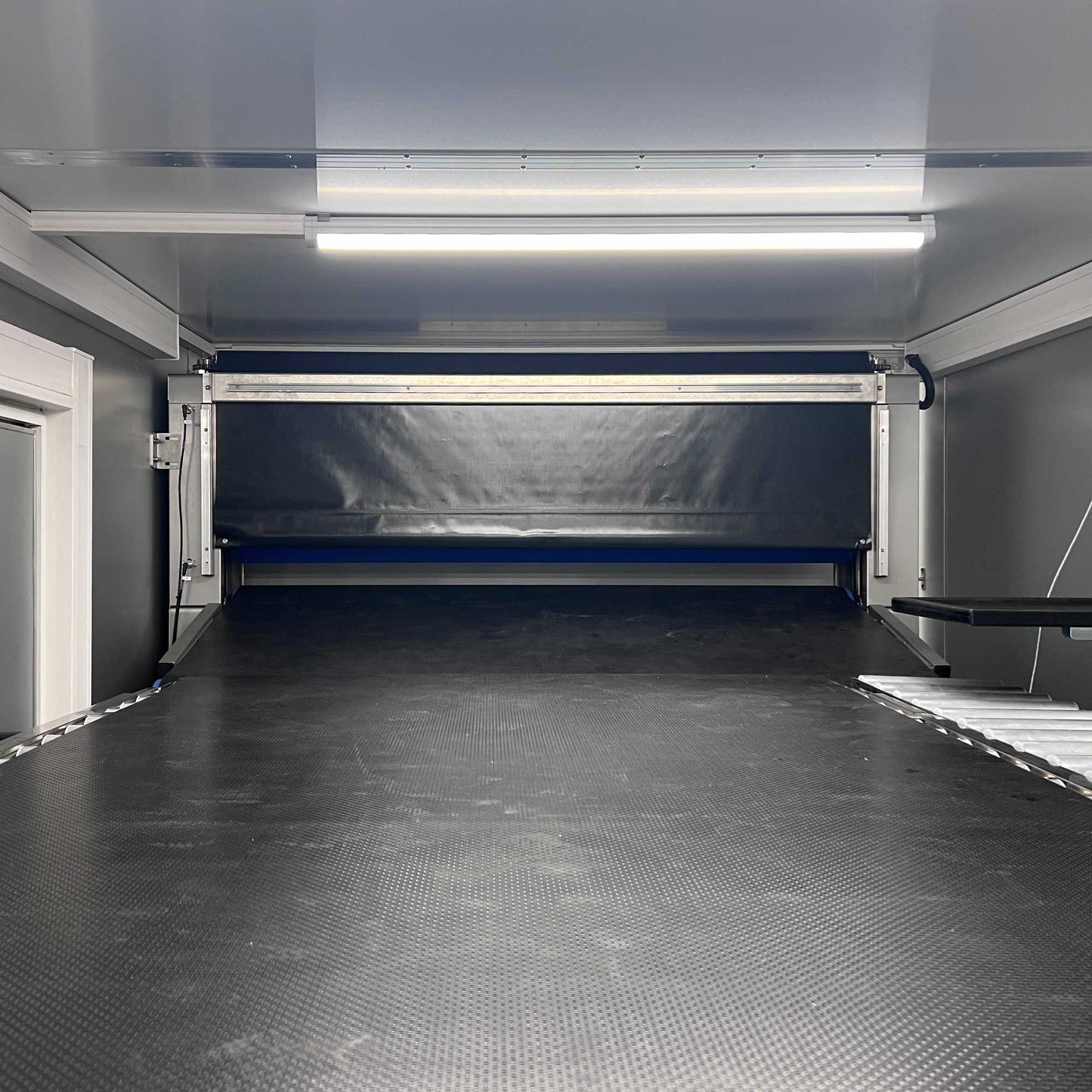
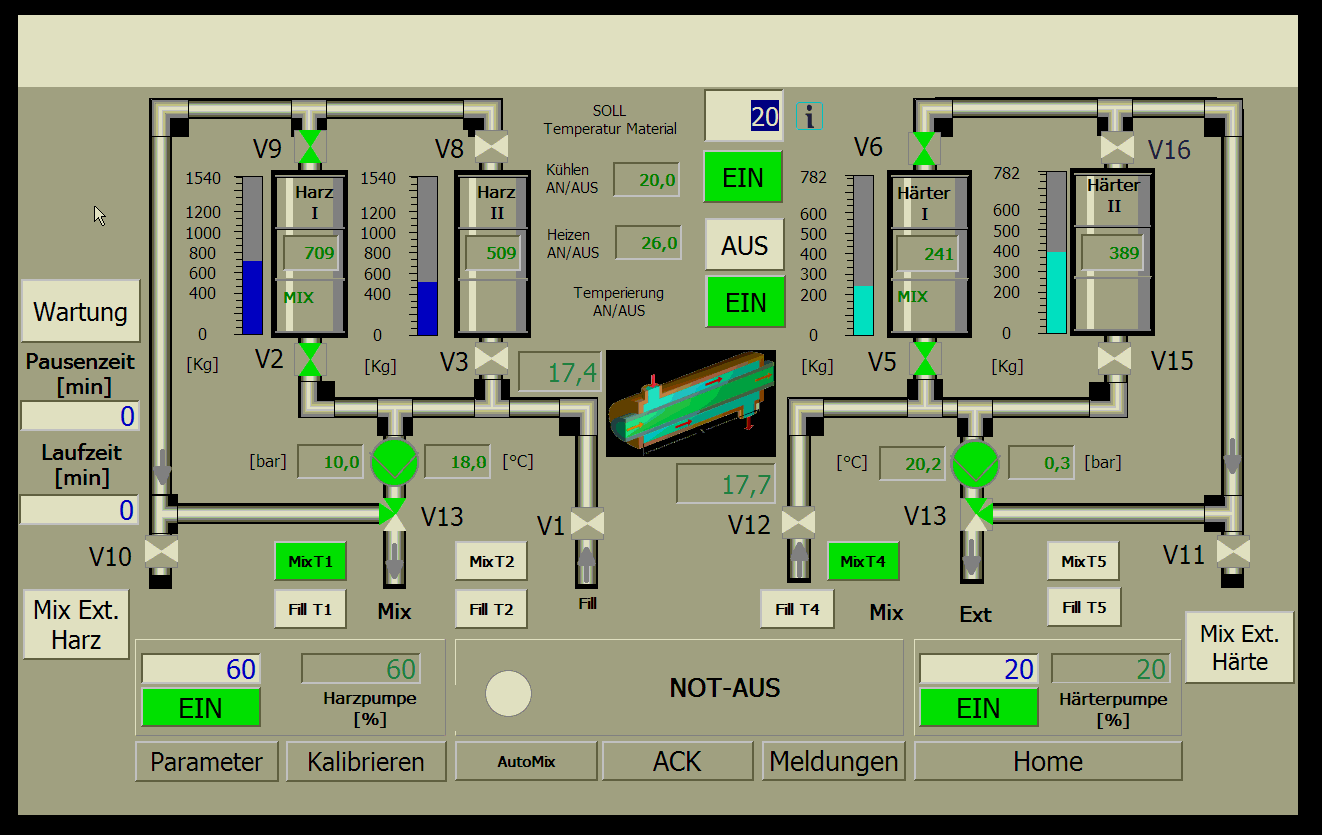
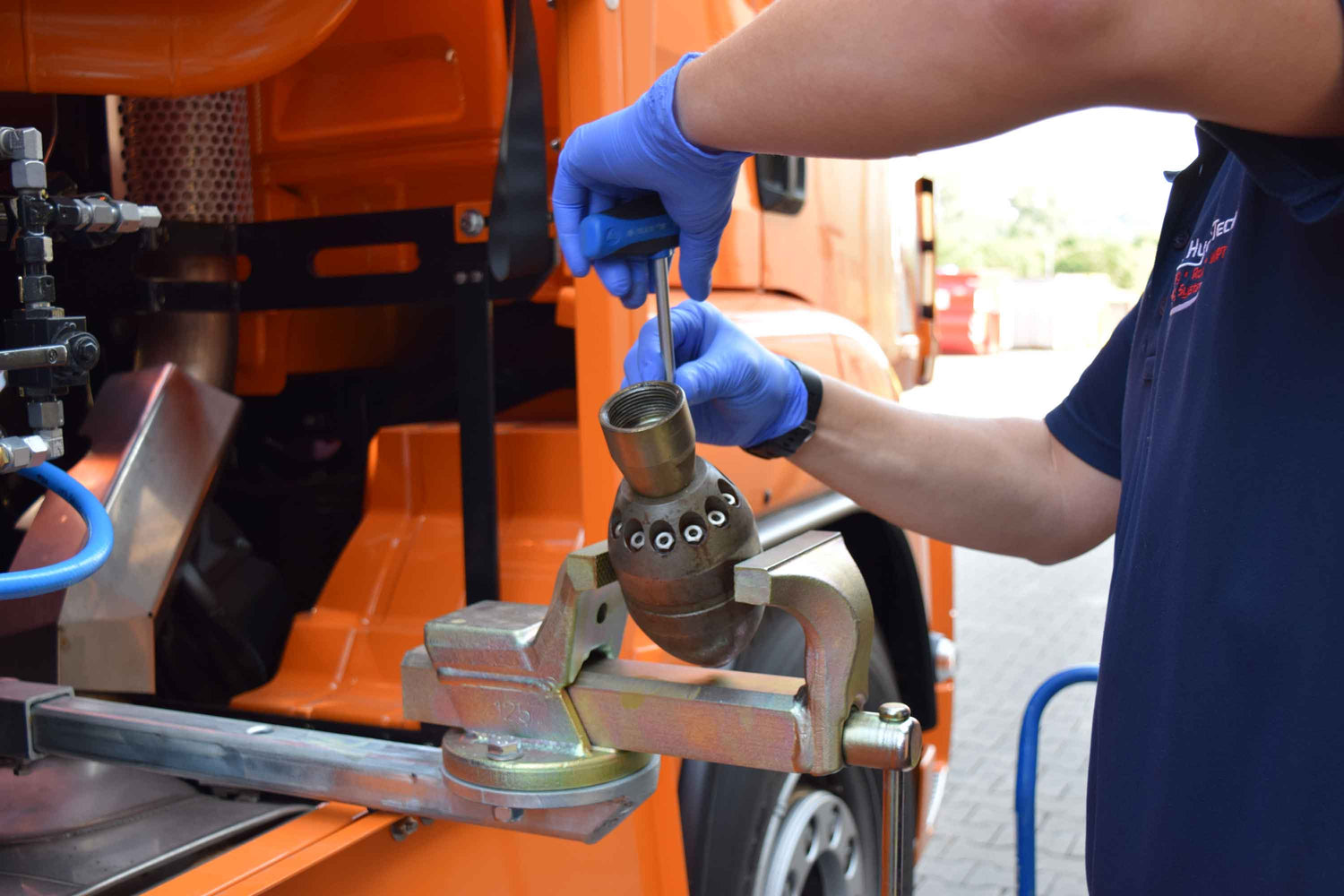