IBG HydroTech GmbH
Steam Units
Steam Units
IBG Steam-units are used for curing epoxy or polyester resin impregnated inliners. Another field of application is the installation of PVC or PE pipes in the forming process. IBG Steam units can also be used as a hybrid system for curing with hot water.
- State of the art PLC – Software (IBG steamcure 1.6) control system
- Industry 4.0 life data plus documentation
- Up to 60 % less oil and energy consumption, thanks to the optimized efficiencies programming of the IBG steamcure
- stainless steel piping
- 10 years warranty on stainless steel pipes
- 2 years warranty on the complete system
- 24/7 worldwide service support through online access by IBG technicians
- Compact design up to 2000 kg/h steam for inliners up to DN 2.100 (84 inch)
- TÜV tested & certified steam components and welding seam
- All system components are driven by frequency converter (low energy input)
- IBG hybrid system for steam & boiled water
- More than 220 steam units worldwide delivered.
IBG steam units can be used for the rehabilitation of DN 50 – 2.000 mm / 2” to 80”
pipes and are made entirely of components with steam certification. They are according to customer requirement and challenges on the construction site. The models are therefore available in different sizes and designs.
Technical Standard
State of the art PLC – Software (IBG Steamcure 1.6) control system Incl. SIEMENS SPS-7 hardware and internet access
- Industry 4.0 life data plus documentation
- Two years warranty on the complete system
- Compact design up to 1200 kg/h steam ( BTU) for inliners up to DN 2.100 (84 inch)
- TÜV tested & certified steam components and welding seam
- Feedwater tank with energy recovery
- Water treatment with double unit, for continuous operation …
- Oil- and water tanks. Size according to customer requirements
- Sensors for pressure; temperature; laminate temp.; water & oil consumption; water and fuel level.
- Stainless steel piping and safety valve with guided media outlet
- B-Station incl. trolly. B station with control valve; PLC control; radio connection to A station; battery with charger and exhaust system. Extremely quite due to patented exhaust muffler. Condensate line with 3 mtr. hose. Warning light (flasher).
- Wireless remote control with emergency stop
- Set of lances and steam hoses (3 x 5 mtr) with coupling
- Standard version suitable for operating temperature up to 130 °C (266 °F).
- Internal/external lighting
Optional
- Inversion unit for additional steam hose (DN 80) into the inliner.This allows faster and more even heating of the inliner laminate
- Radio remote control and camera monitoring
- Wireless remote control with emergency stop
- Chiller unit for controlled cool down sequence
- Add-on system for second Blower with electronic switch box
- IBG hybrid system for steam & boiled water
- Integration of additional temperature sensors (laminate) over the entire inliner length Version
- Version up to 180°C (356°F) operating temperature
Technical Data
Notice: 1 bar = 14,5 psi 1 kg steam = 2.418 BTU
TYPE Kg steam/h |
Max DN In inch-mm |
Standard |
Power Cons. In KW incl. 1 or 2 Blower |
Oil Cons. average per hour in ltr.
|
PLC control and remote control |
St.Steel piping + steam certified components |
Industry 4.0 standard with life data |
B-Station with 400 mtr. wireless connection |
400 |
20 - 500 |
1,25 |
20 |
20 |
✅ | ✅ | ✅ | ✅ |
800 |
32 – 800 |
1,0 |
25 |
35 - 45 |
✅ | ✅ | ✅ | ✅ |
1.200 |
40 – 1.000 |
1,0 |
30 |
50 - 60 |
✅ | ✅ | ✅ | ✅ |
1.600 |
56 – 1.400 |
1,0 |
45 |
70 - 80 |
✅ | ✅ | ✅ | ✅ |
2 x 1.000 |
84 – 2.100 |
1,0 |
55 |
95 - 105 |
✅ | ✅ | ✅ | ✅ |
IBG INV Drum 2.200 – DN 1.200 in sea container 20 ft, with Swivel system device +-90 for the INV drum, plus steam unit 1.000 kg/h.
Software: IBG Steamcure® 1.6
![]() |
![]() |
The software IBG steamcure® 1.6, is used for reliable installation and documentation of inliner in pipe system. The software enables the control of the optimal energy input as well as the automatic regulation of the curing parameters. This permanent calculation of the optimal parameters regarding steam quantity; air quantity; volume flow rate; temperature and pressure would not be possible with a manual operation and an energy input reduction of up to 60% would be unachievable. Due to the Industry 4.0 standard, a permanent documentation of the process parameters (if requested via Internet connection with real-time data transmission) is carried out, which forms a determining basis regarding the QA standards. This is the basis for reproducible construction site quality. Also of high importance is the wireless connection of the B-Station (incl. battery pack), which allows a continuous control of the outlet valves (pressure and temperature) without additional personnel on site. The software is available in all common languages and technical units (of measure).
![]() |
![]() |
Training: IBG steamcure® 1.6 & Steam-units
BG offers basic training for all systems at our training center in Alzenau. In addition, all system operators are accompanied and trained by IBG technicians on a construction site assignment. This makes it possible to avoid initial application problems and creates confidence among the employees. Also in the further course of application, our technicians are available for problem solutions via internet access at any time. This avoids considerable travel costs and the response time is extremely short. The "plug&play" system design of IBG HydroTech also has a positive influence on this, enabling the user to easily replace components on site in the event of damage. Supplementary training courses can also be requested from our service office at any time.
3D Project View
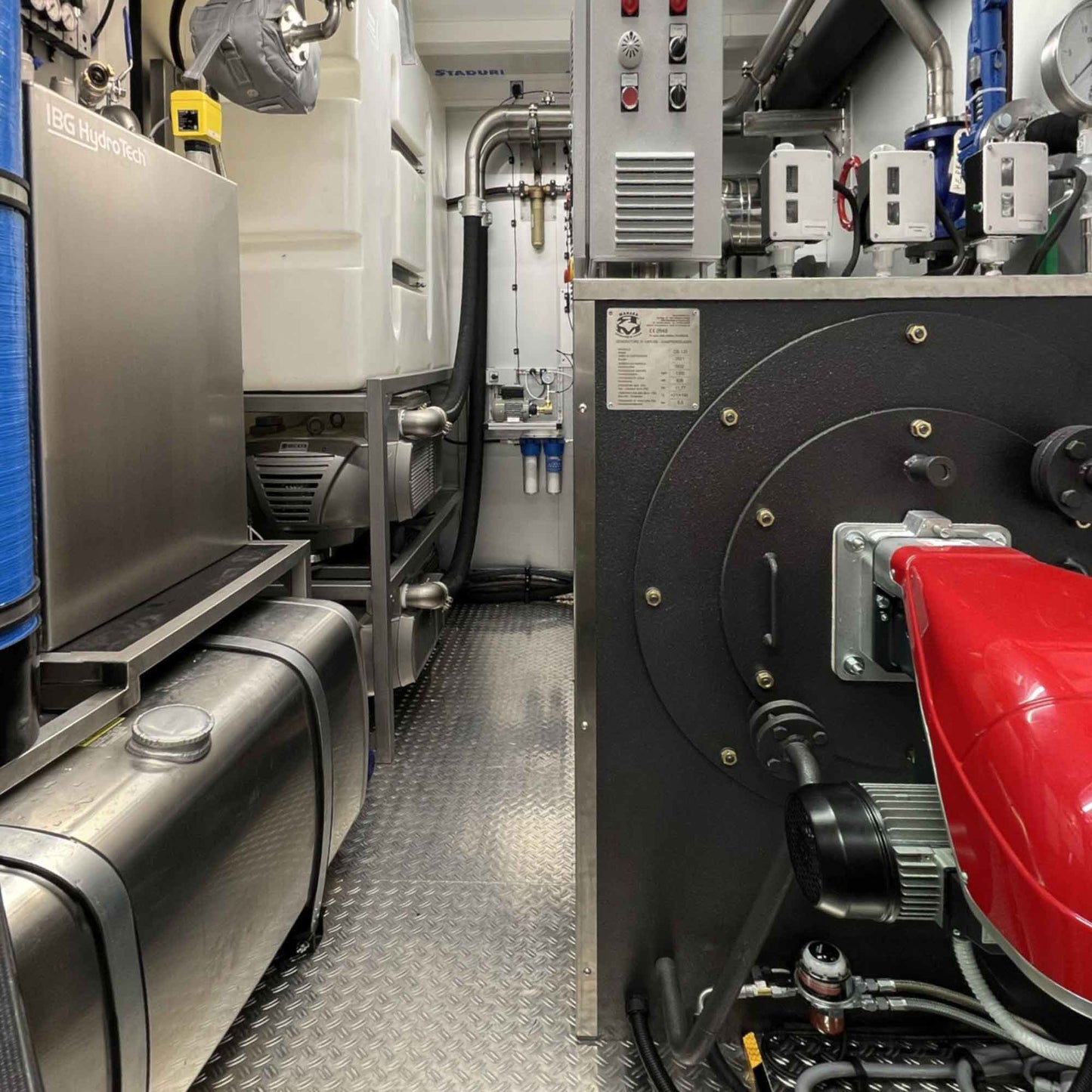
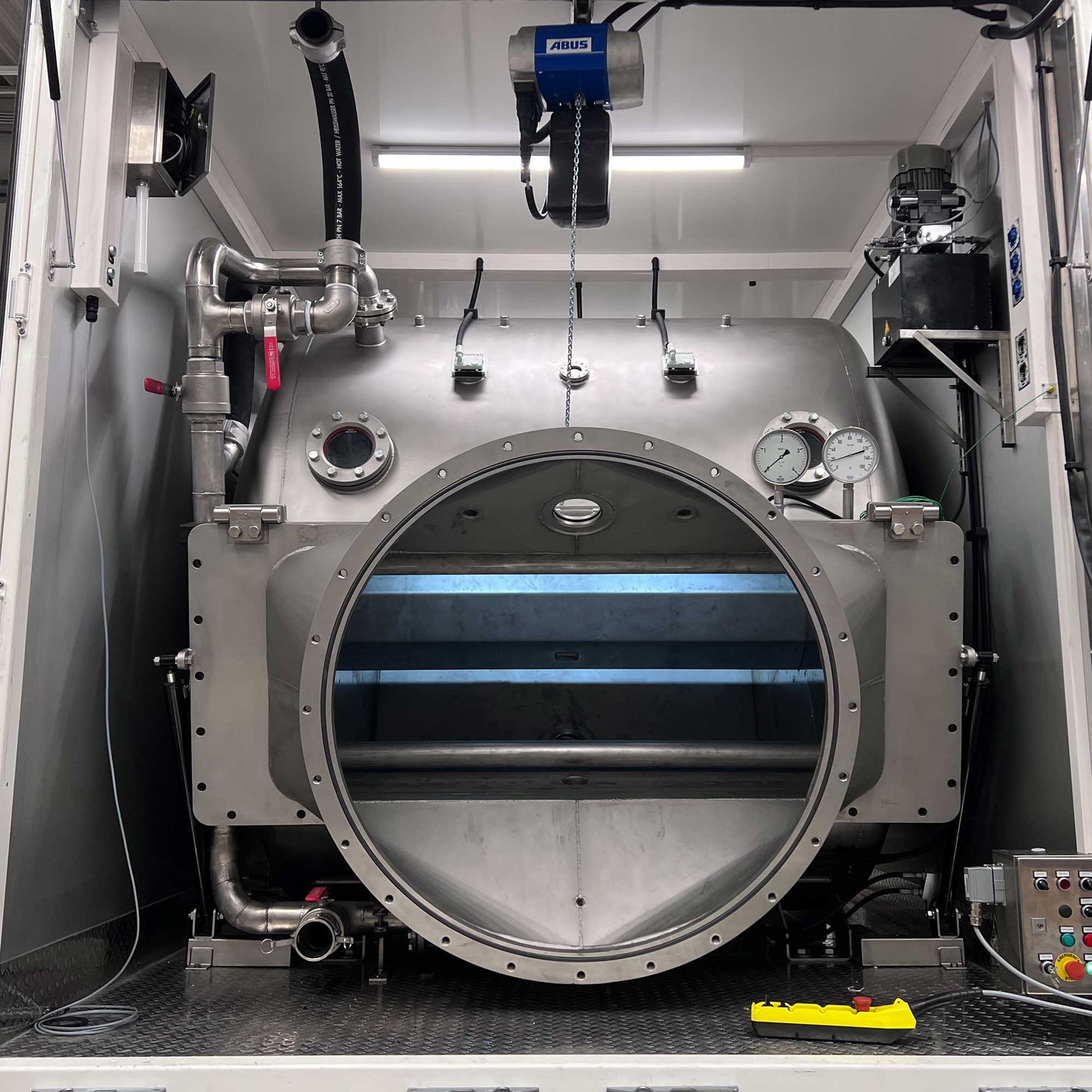
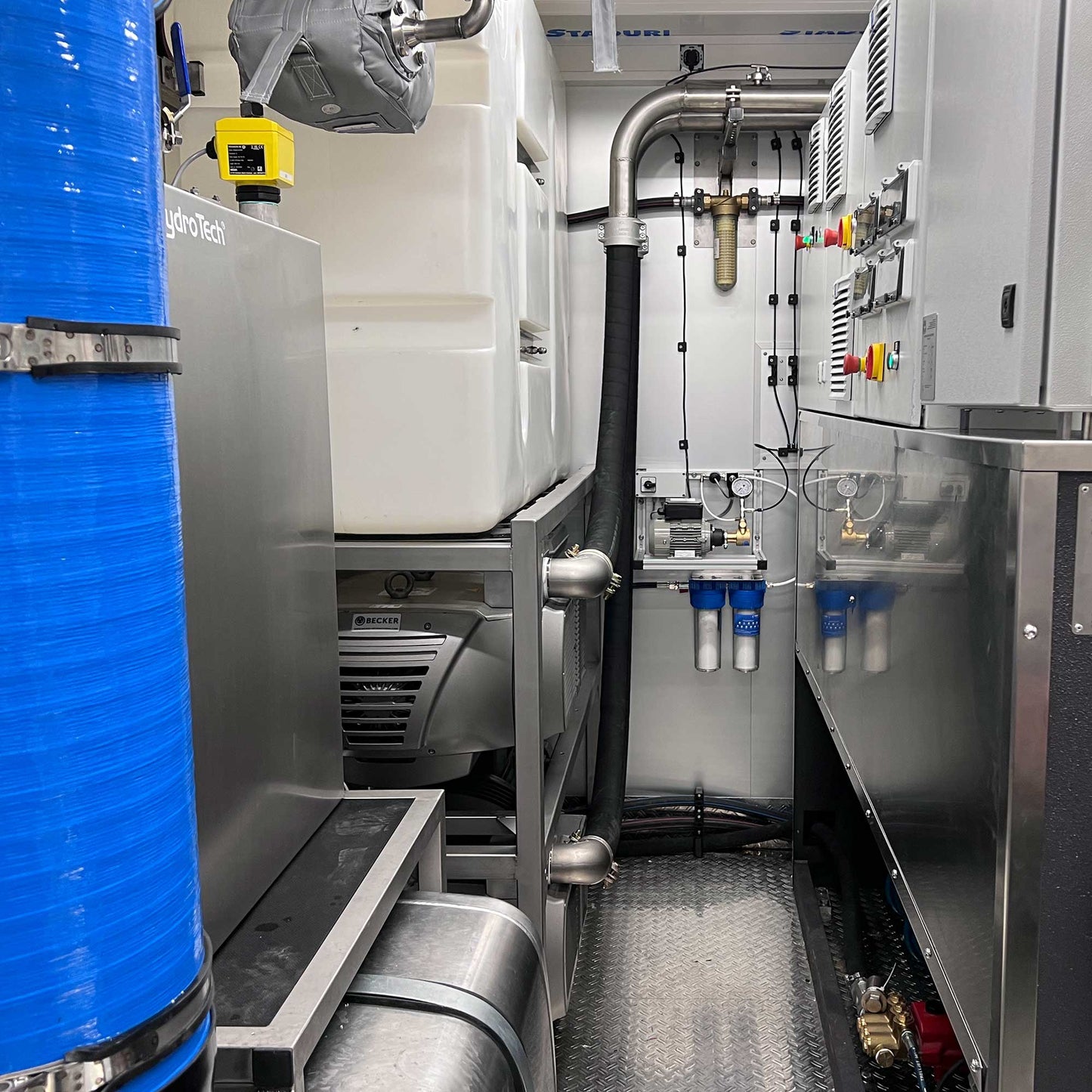
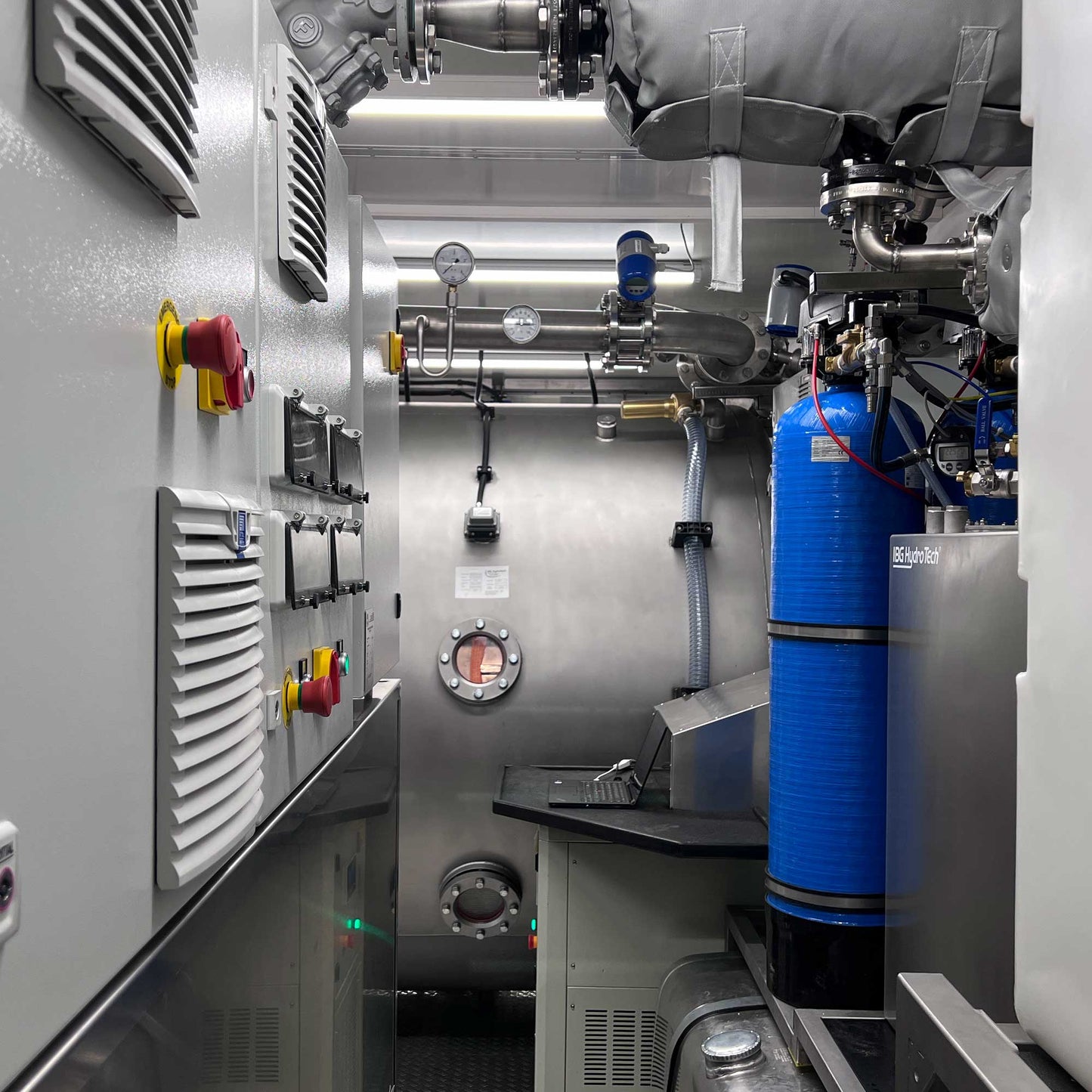
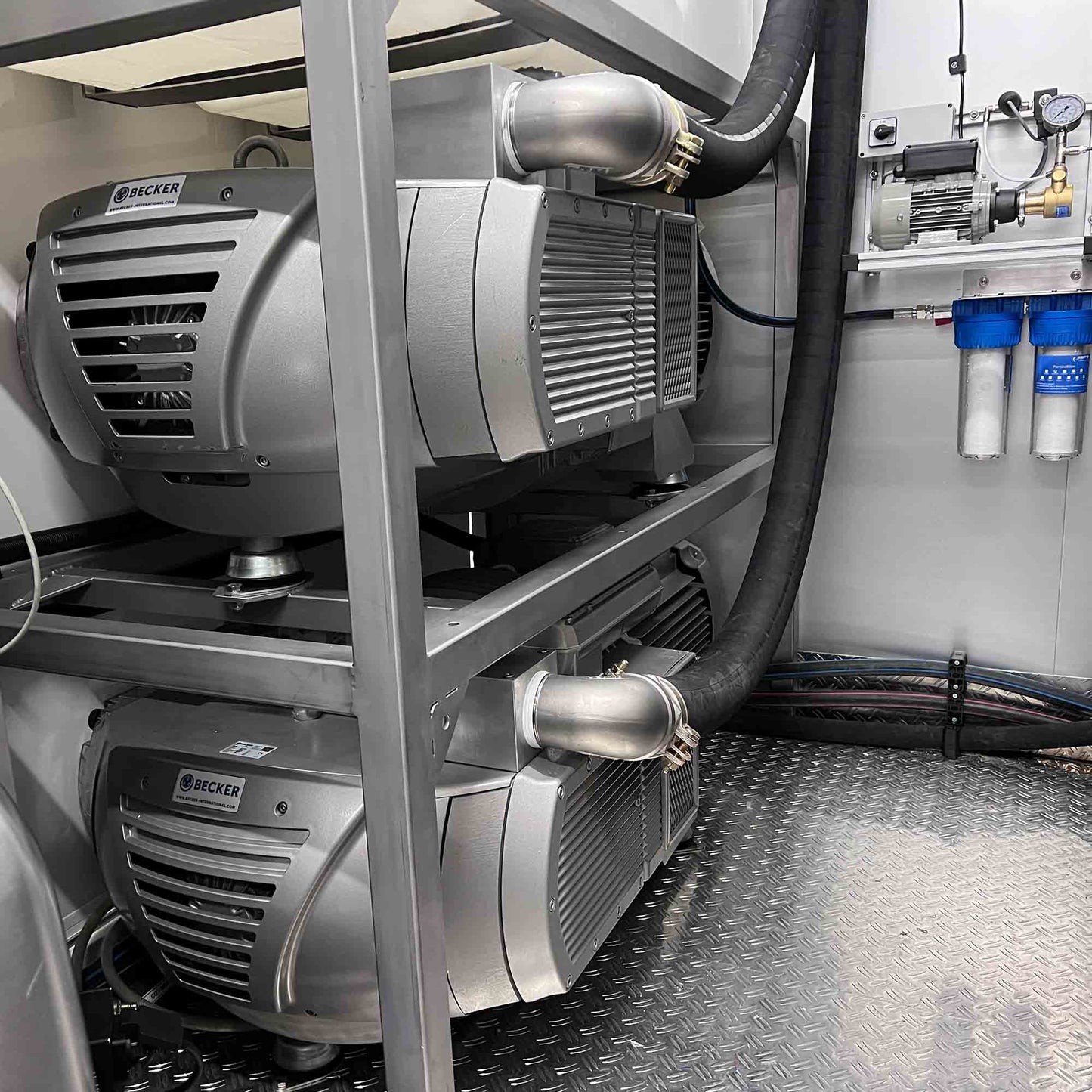
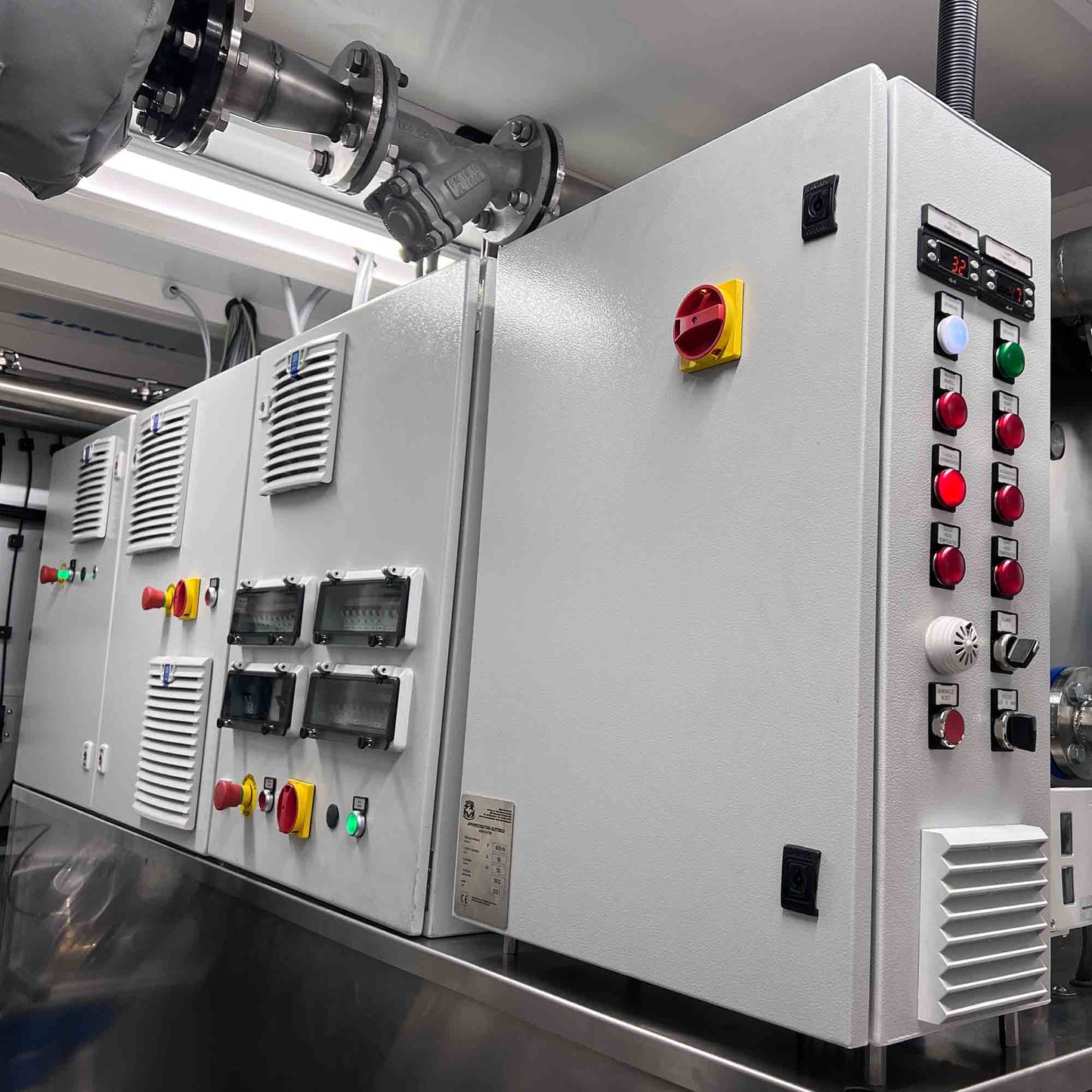
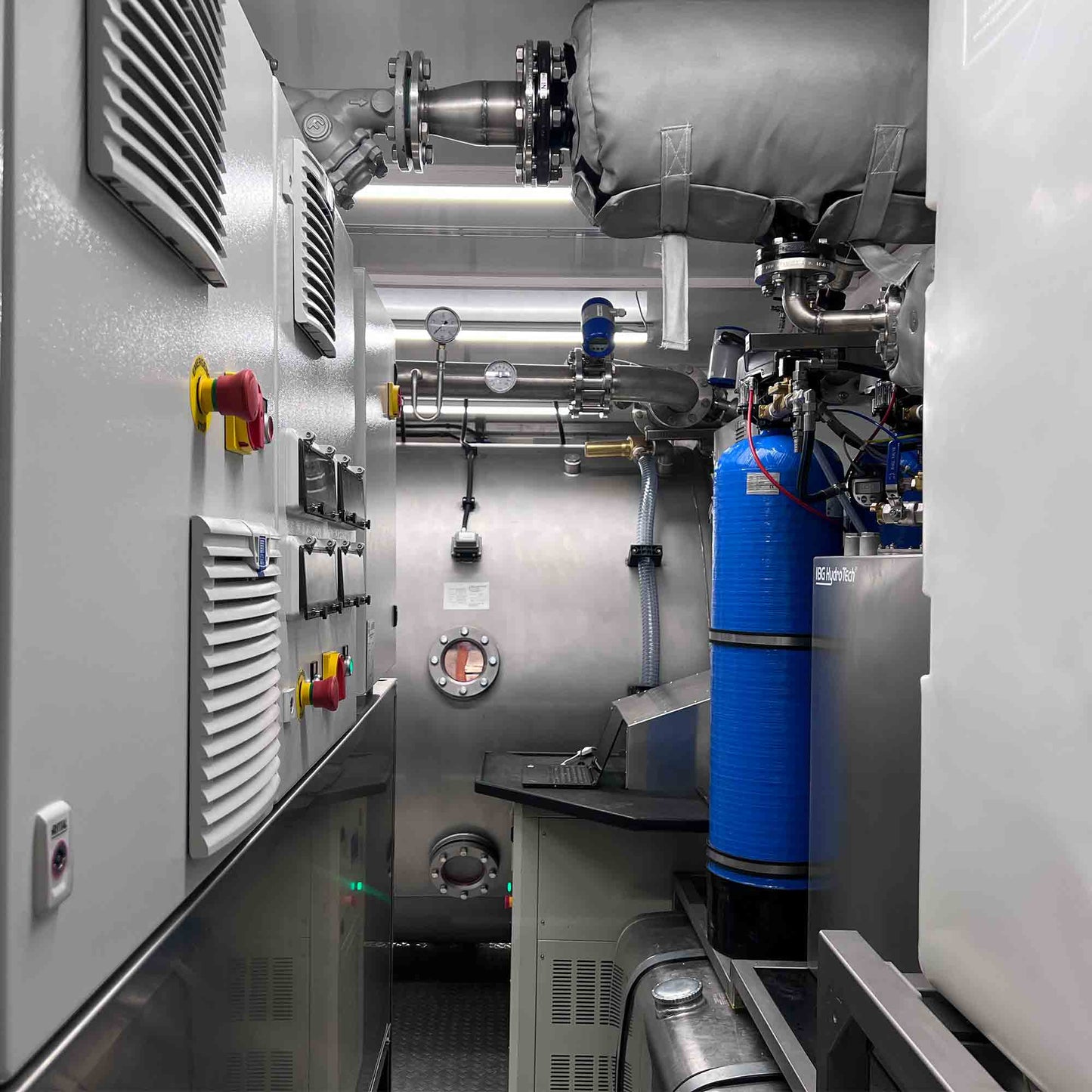
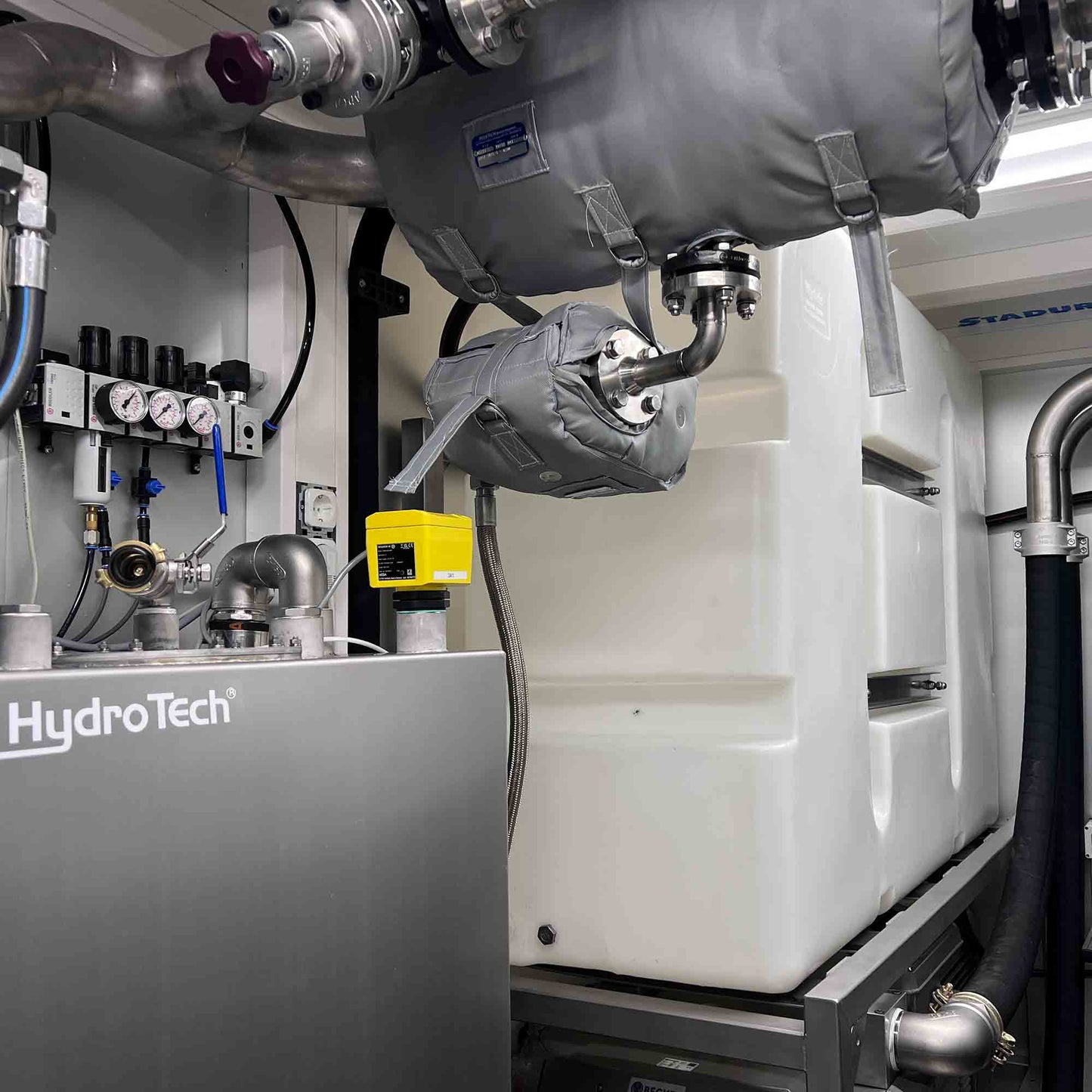
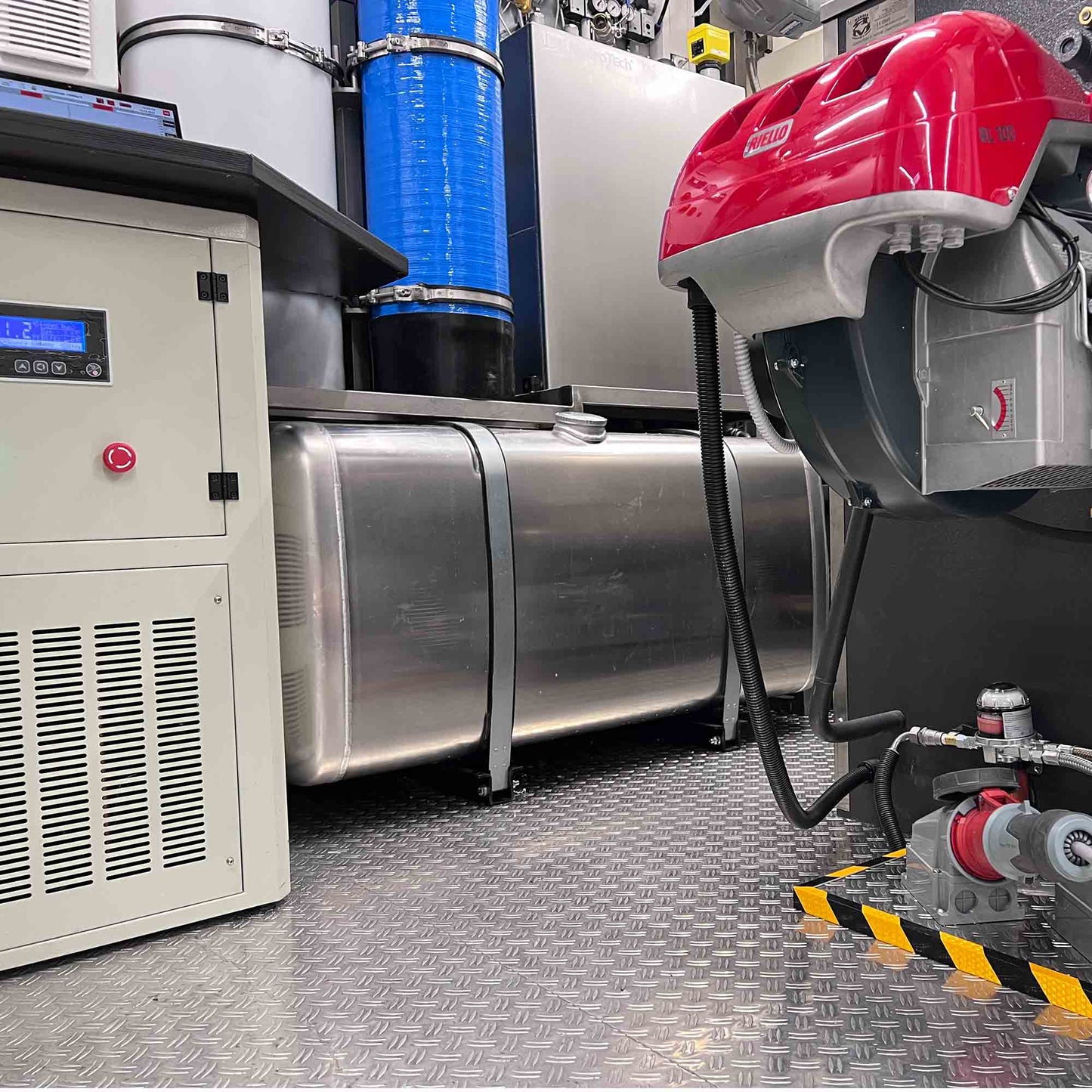
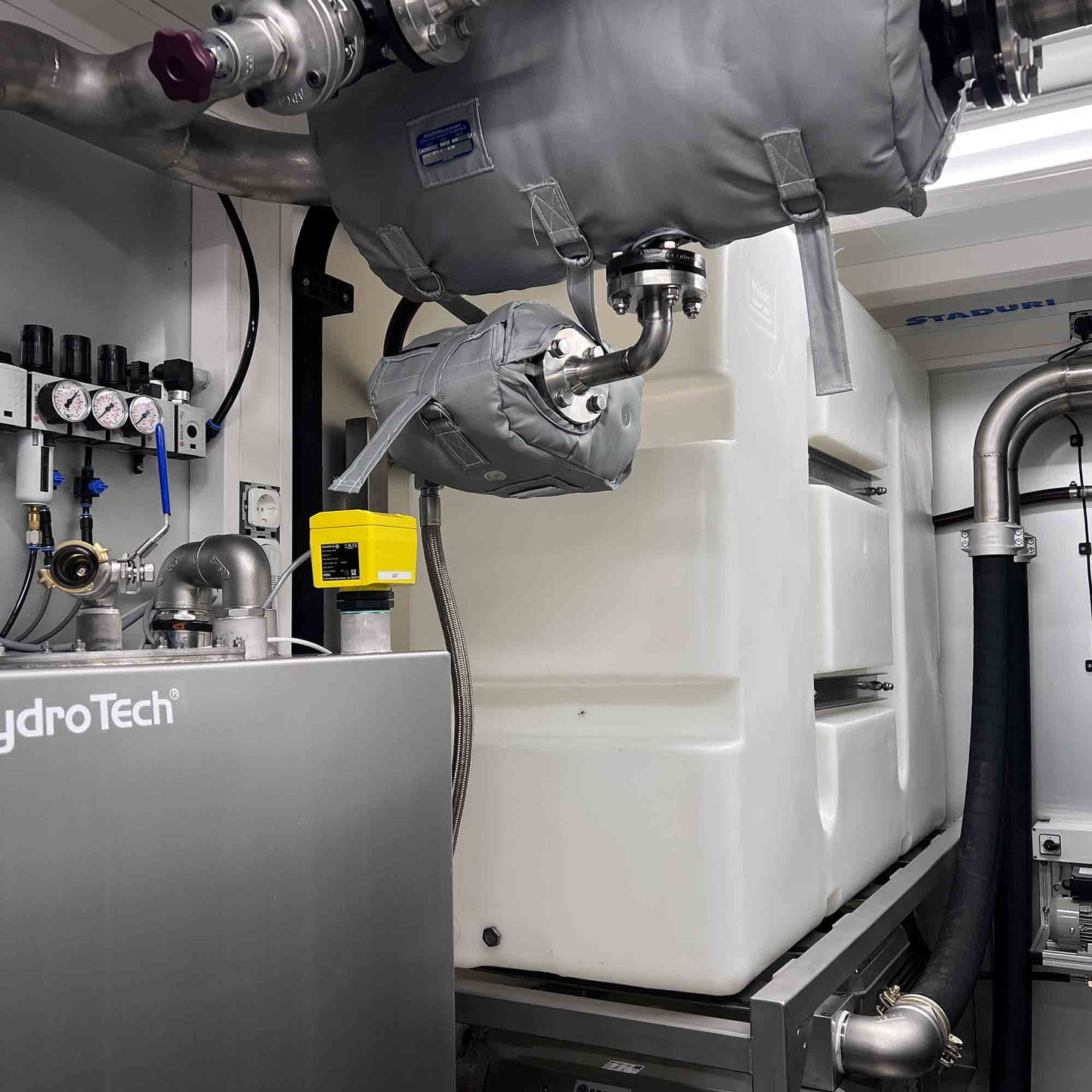
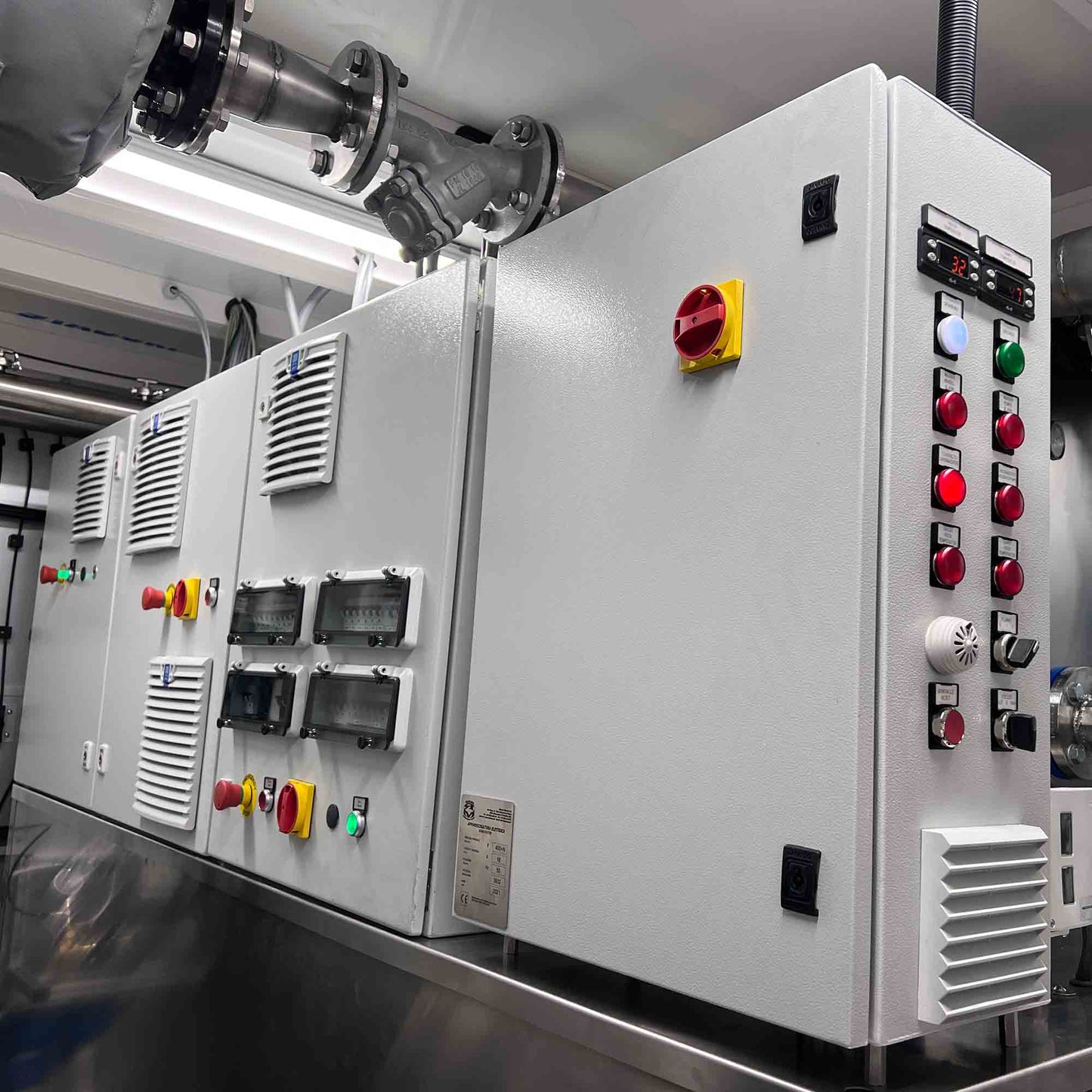
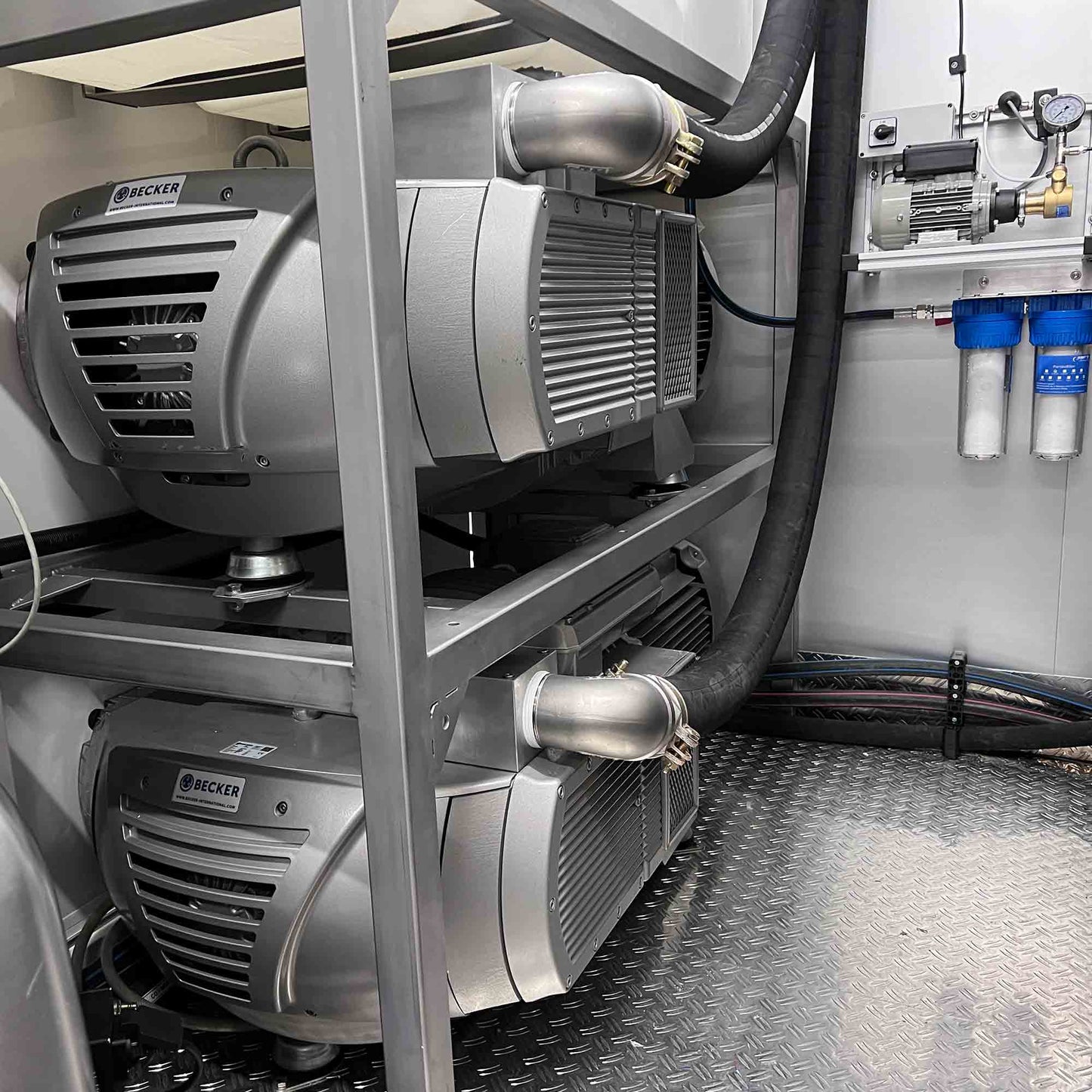
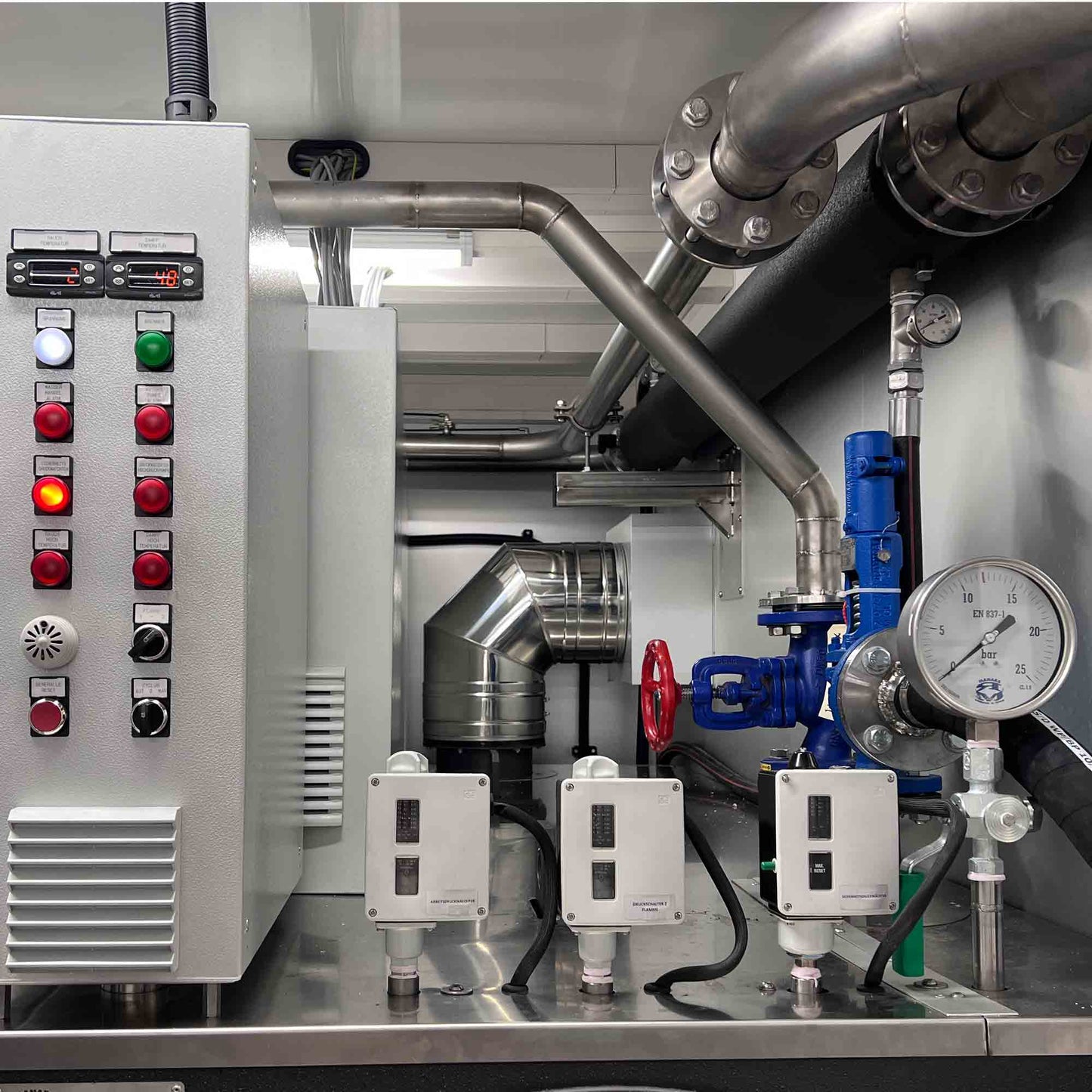
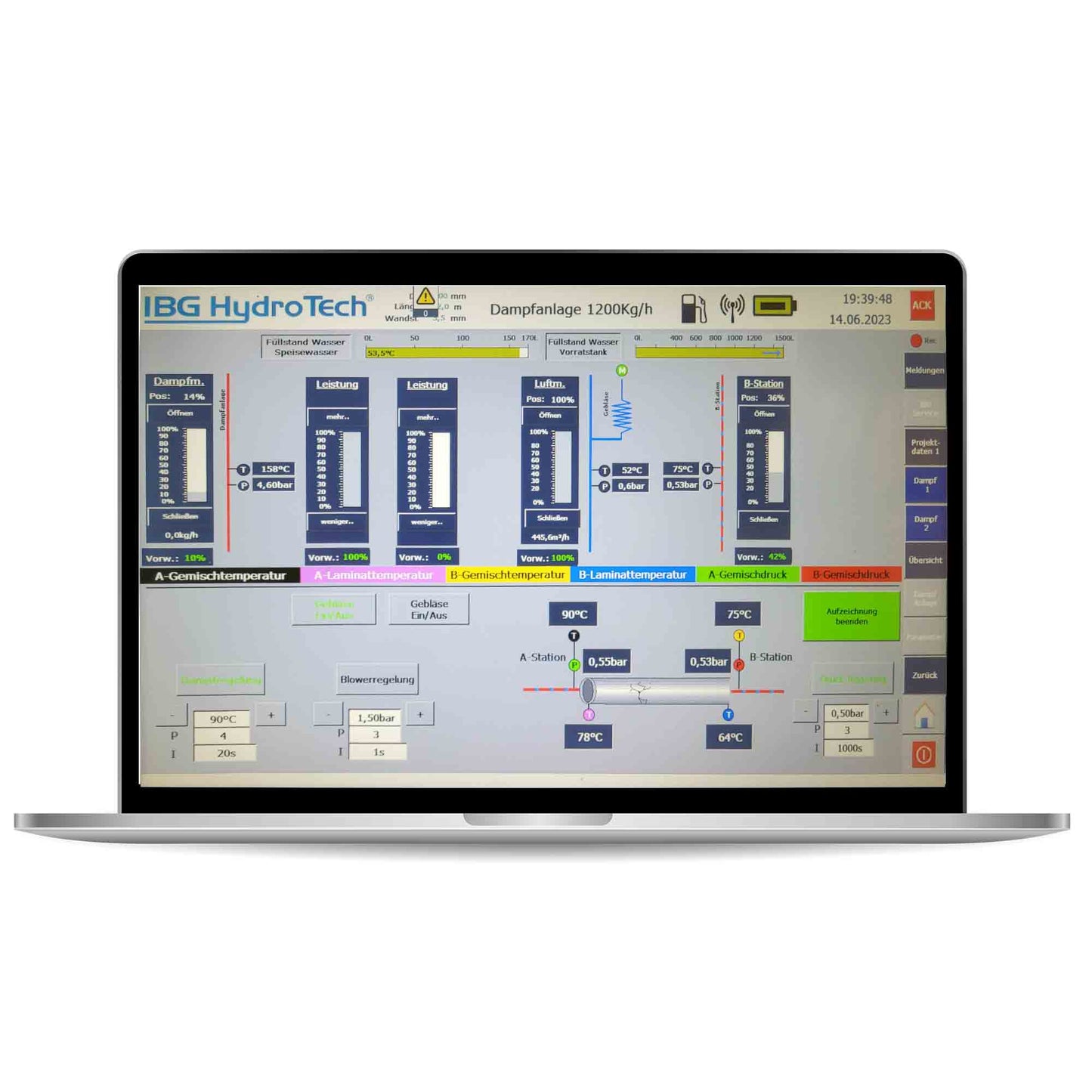
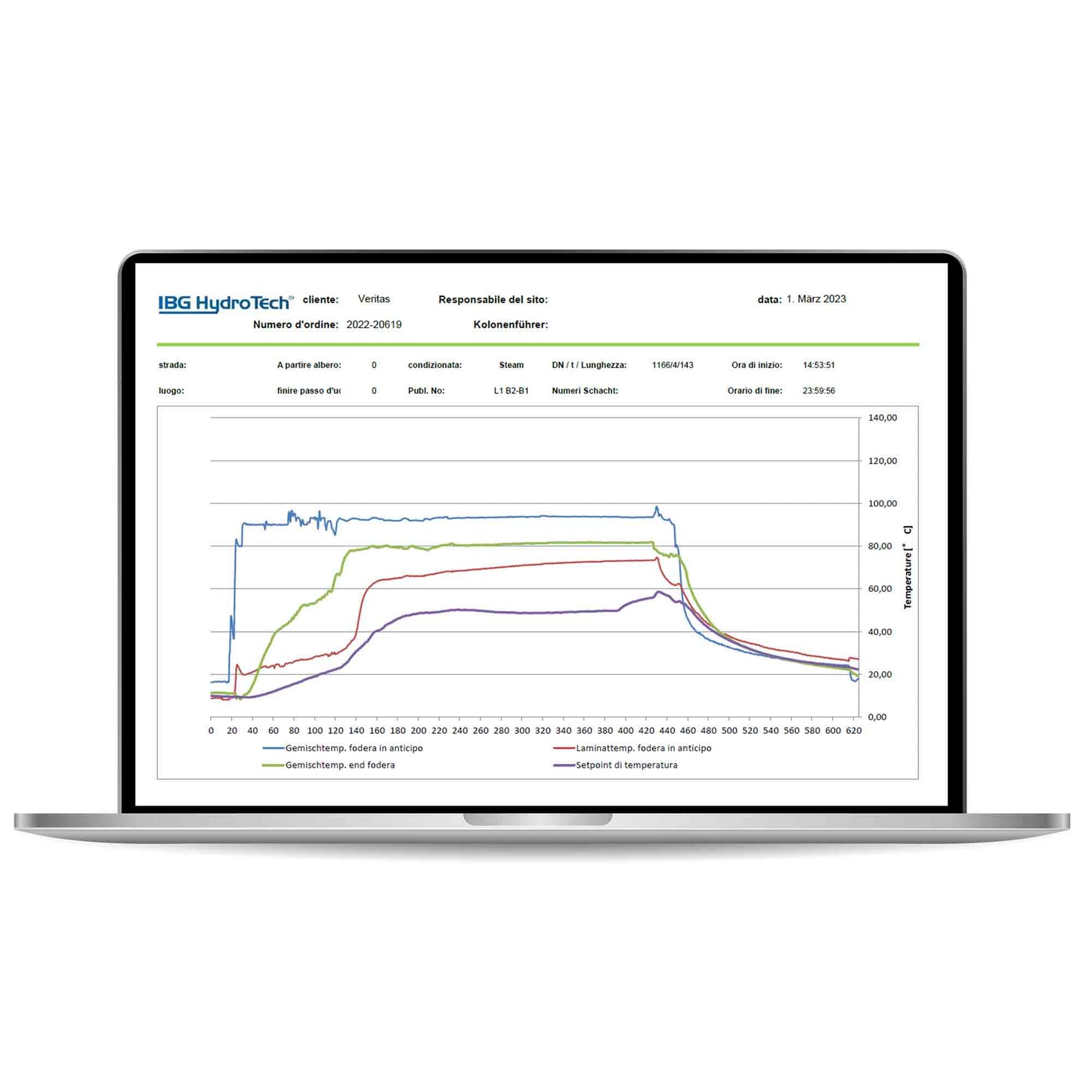
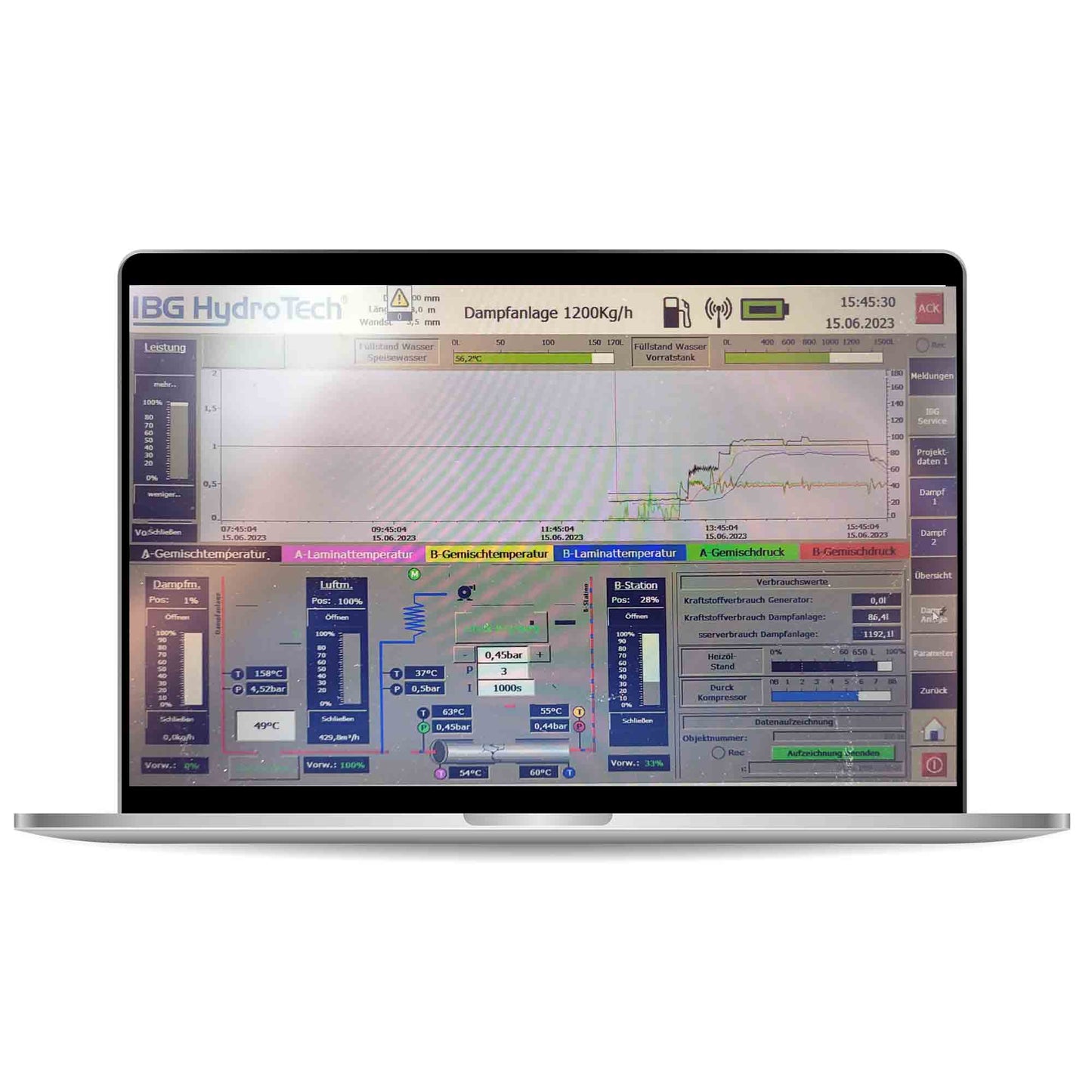
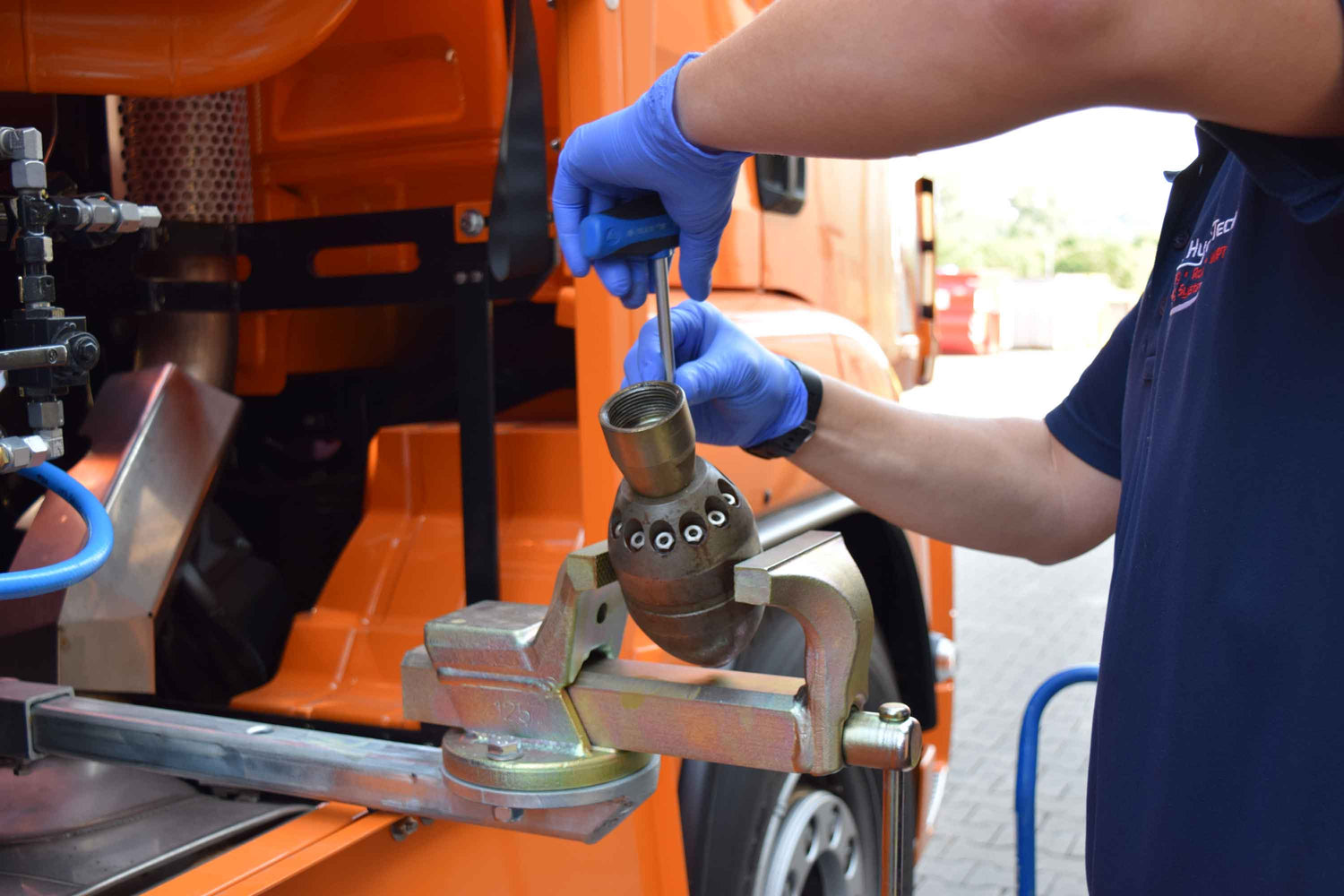